
Sample Projects
Conveyor Design

ALCOA Rockdale, Texas, USA
Commissioned in 2005, this 19.3 km single flight conveyor was the longest conventional conveyor in the world. It also included one intermediate drive and 11 horizontal curves. In order to negotiate 11 horizontal curves, power was distributed between the head, tail, and halfway point on the conveyor. The intermediate drive is one of the first of its kind on a surface operation. OCC provided intermediate drive support as well as the control algorithms for starting and stopping.
Date
Commissioned 2005
Role
Designer
Client
Thyssenkrupp Robins
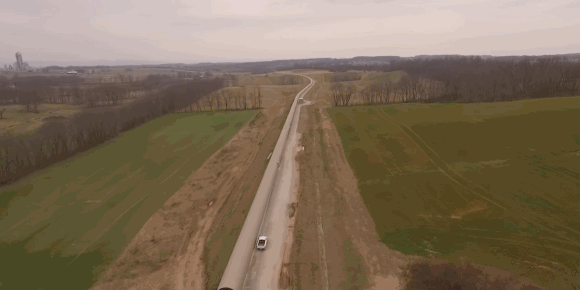
Lehigh Cement, Union Bridge, USA
Overland Conveyor Company was selected as the owner's technical representative for this 7km overland conveyor carrying 2500 mtph of crushed limestone. Snaking through populated areas of rural Maryland, this conveyor includes 5 horizontal curves and 27 vertical curves. OCC developed the design used to select the contractor and supported Lehigh through detail design and commissioning.
Date
Commissioned 2016
Role
Owners Consultant / Designer
Client
Lehigh Cement

Reliance Sasan UMPP, India
Overland Conveyor Company designed the 14 km overland conveyor from the port to the new Ultra Mega 3960 MW power plant. The overland includes head and tail drives with two horizontal curves. The project required significant cooperation between diverse multi-national engineering teams.
Date
Commissioned 2014
Role
Designer
Client
Northern Heavy Industry China
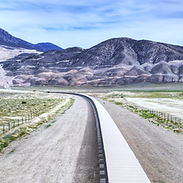
Barrick Gold, Cortez Hills, USA
Overland Conveyro Co was selected to provide specialized design and commissioning support for the development of unique and custom control algorithms for an 11.6 km overland conveyor. The system consists of several individual conveyors totaling over 14.5 km in length with the 11.6 km centerpiece curving horizontally down a large hill. Conveyor capacity is set at 1000 tons per hour.
Date
Commissioned 2009
Role
Designer
Client
Thyssenkrupp Robins

Heidelberg Cement, Cadman, USA
This downhill conveyor was designed for Cadman's new limestone quarry in Washington state. The conveyor handles material in both directions and is designed to carry 1000 tph down the hill and 400 tph back up the return side. It overcomes difficult terrain over its length of 2 km, including a vertical drop of 274 m with 14 vertical and 2 horizontal curves, and a maximum slope of 18 degrees.
Date
Commissioned 2006
Role
Designer
Client
Thyssenkrupp Robins

Chinalco, Toromocho, Peru
Overland Conveyor Company was selected to provide preliminary design, technical bidding documents and bid review to Aker Solutions (working for Chinalco) for the 10 km conveyor from this greenfield mine to processing plant over the Andes Mountains. The conveyor reaches elevations of 5000 m, and OCC's design featured a unique mid-drive solution which reduced overall conveyor capital cost by approximately 40%.
Date
Commissioned 2013
Role
Designer
Client
Aker Solutions
Studies
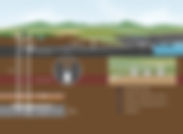
Sirius Minerals, North Yorkshire, UK
Sirius Minerals' Woodsmith mine targets the extraction of polyhalite, a unique multi-nutrient fertilizer. Sirius Mineral's selected thyssenkupp and Overland Conveyor Company to provide a design study for the design and budgetary costing of a 37 km, single flight, underground conveyor to transport material from mine to processing facilities near the port. OCC supported both thyssenkrupp and Sirius minerals with the difficult balance of mixing long distance conveying with the underground environment.
Date
Design Study 2016-2018
Role
Designer
Client
Thyssenkrupp
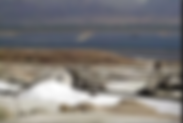
Dead Sea Works, Israel
In 2012, the Israeli government made plans to fund and implement the Dead Sea Salt Recovery Project. a permanent solution for stabilizing the water level of the Dead Sea Works' Pond #5. The solution includes removing 20 million tons of salt annually and transferring it 25 km to the northern basin of the Dead Sea. OCC was selected to supply overland conveyor technology to the project study team. Project options included multiple conveying technologies and single flights over 20 km in length.
Date
Design Study 2015
Role
Designer
Client
Dead Sea Works

Tarong Transport Alliance, Australia
The Tarong Transport Alliance selected Overland Conveyor Company to design a belt conveyance system for a 71 km long haul. This ground breaking 71 km system consisted of three flights of 30 km, 30 km, and 11 km would include the 2 longest single flights in the world. They included intermediate drives and horizontal curves to fit within a narrow corridor between Tarong and the New Acland coal supply.
Date
Feasibility Study 2007
Role
Designer
Client
Tarong Transport Alliance

Rio Tinto, Simandou, Africa
Overland Conveyor Co researched and evaluated Doppelmayr's proprietery RopeCon technology for its application for a project conveying over 9000 mpth of material over extremely difficult terrain from mine to rail loadout.
Date
Design Study 2012
Role
Designer
Client
Doppelmayr
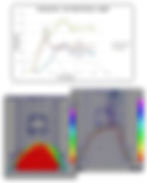
Hamilton County Coal, Illinois, USA
Overland Conveyor Company performed a feasibility study on a stacking tube throughput tonnage. The stacking tube window height and shape of the sills were modified to observe the corresponding flow rate. Off center loading into the stacking tube was considered to analyze the throughput difference between windows.
Date
Feasibility Study 2017
Role
Designer
Client
Alliance Resource Partners
Transfer Chute Designs & Audits

Torr Aggregate Industries, United Kingdom
Overland Conveyor Company supported Komatsu with troubleshooting, designing, and evaluating 4 transfer chutes that were experiencing continual blocking and plugging potential. DEM parameters were optimized by modeling the existing material build up on the spoon. The 4 transfer chutes were redesigned to alleviate plugging potential and minimize chute wear.
Date
Commissioned 2019
Role
Designer
Client
Komatsu

Mont Wright, Canada
Overland Conveyor Company worked with ArcelorMittal to redesign 8 transfer chutes. Excess chute wear, belt ripping and plugging were observed due to large slabs of material measuring as large as 50 inches or 1270 millimeters. The rockboxes for each transfer had to be modified to adequate space for the large lumps and gently load the receiving conveyors.
Date
Commissioned 2014
Role
Designer
Client
ArcelorMittal

South Flank, Australia
Overland Conveyor Company was selected to design a belt conveyance system and 4 transfer chutes. The emergency stop case was analyzed to determine how the outby transfer chute would handle the surge of material and verify the receiving conveyor could be restarted to draw the material away. Each conveyor was simulated with ramped belts observing full belt speed to an emergency stop based on the analyzed emergency stop time during the conveyor analysis.
Date
Design Study 2016
Role
Designer
Client
Jacobs

Round Mountain, Nevada, USA
Overland Conveyor Company was selected to provide an audit of 2 transfer chute designs. A range of material properties were considered from dry to wet clay and the DEM parameters were optimized accordingly. Gates were installed for redirecting and splitting the material flow to two receiving conveyors. Equal tonnage throughput towards each receiving conveyor was desired and analyzed.
Date
Design Study 2015
Role
Consultant/Auditor
Client
Smith Monroe Gray